National Manufacturing Mission: Building Capabilities through Education and Skill Development
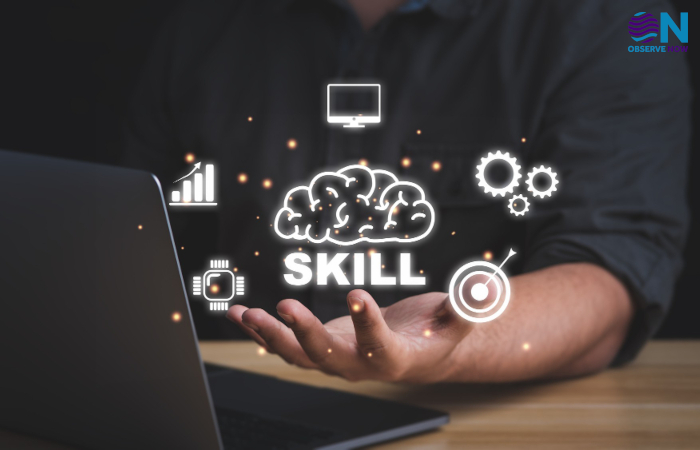
To position itself as a global manufacturing hub, India needs to build a pool of skilled workers. However, coupled with the transition to Industry 4.0, which is rewriting the whole of the manufacturing ecosystem with next-gen automation technologies like AI, robotics and data analytics, the workforce issue becomes an increasing priority. Skill development and education lie at the heart of industrial development in making sure that the workforce in India can serve the needs of the future. The National Manufacturing Mission is one of the prominent initiatives to bridge the existing gap in skills and make India a competitive player on the global manufacturing map.
The Role of Education and Skill Development in Driving Industrial Growth
In a rapidly evolving tech landscape, education and skill development are key drivers of industrial growth. A well-trained workforce contributes to innovation, efficiency gains, and competitive advantage that sustain industries, going far beyond advances in production. If India is to become a key global manufacturing hub, it must cultivate a workforce that is skilled in emerging technologies like AI, ML, robotics, cloud computing and data analytics.
Aligned with the goals of the National Manufacturing Mission, India has been revamping the curriculum of its educational institutions to incorporate emerging technologies like these. India will be able to develop a pool of skilled professionals who possess a deep understanding of the tools and technologies that drive Industry 4.0 by equipping students with both theoretical knowledge as well as practical experience of working with these next-generation technologies in manufacturing processes.
The Need for Skill Development in Manufacturing
Workers skilled in automation, smart manufacturing and other high-tech disciplines are in increasing demand in Industry 4.0. But as studies show, one-third of India’s workforce is not in a position to take on jobs of the future. The gap between academic knowledge and industry needs is posing serious problems for manufacturers and enterprises that struggle with a lack of skilled personnel that threatens their ability to profit.
Technologies like robotics, AI, digital twins, data analytics, and others will power the future of manufacturing. Industries need those who know how to run and create in these digital ecosystems. This means equipping the workforce with both technical skills and problem-solving skills that can be leveraged as the industry shifts towards smarter, more automated production.
Government Initiatives Supporting Manufacturing Skills
The Government of India, realizing the need for a skilled workforce, has taken several initiatives to up skill the youth for Industry 4.0. One such initiative is the Skill India Mission which aims at developing workforce capable of meeting the demands of the modern industries. It covers everything from traditional manufacturing practices to next-generation tech like AI and robotics.
A second touchstone of India’s strategy to build a skilled workforce is collaboration among government, academia and industries. Many institutes, such as Indian Institutes of Technology (IITs), National Institutes of Technology (NITs) and Industrial Training Institutes (ITIs) have already initiated demand-based programs focusing on specific skills to bridge this gap. To meet the technological needs in manufacturing, there is increasing incorporation of Industry 4.0 focused subjects and courses in manufacturing schools.
Skill Development in India also needs Public-Private Partnerships (PPP) in place. A significant skilled based initiative for bridging the gap between academic and industrial need is the Prime Minister’s Internship Scheme through which elite companies offer intern opportunities to the youth. This is a scheme which gives students real, practical experience and allows them to accumulate business experience in the field. Alongside various other methods that can contribute to building an agile, active and unfulfilled learning shelf in the country, this step will go a long way in building an agile and competent workforce for the future demands of the country.
Institutions work in collaboration with industry leaders and educational organizations to design training programs that meet actual industry requirements. Such collaborations help students gain exposure to real-business hands-on activities, thus making them industry-ready.
The Role of Digital & Emerging Technologies
With Industry 4.0 making its way towards India, the importance of digital and emerging technologies in the skilling of human resources is immense.
The shift to digital technologies in training programs will expand access to and participation in a more scalable learning model. Leveraging online tools, virtual simulations, and partnering with industry will broaden the reach and efficacy of skill development programs to ensure that workers across India’s vast landscape are trained for the future.
Future Roadmap: Continuous Learning Ecosystem
With a fast-evolving tech landscape, India needs to become a continuous learning ecosystem. This ecosystem should be flexible to meet the evolving demands of the manufacturing industry and promote lifelong learning. Because technology is developing quickly these days, workers will need to constantly improve their abilities in order to stay relevant.
Conclusion
The National Manufacturing Mission is an important milestone in making India a global manufacturing hub. This mission’s foundation is education and skill development because human resources are the principal asset of a country to adopt and implement advanced manufacturing technologies. Through initiatives like the Skill India Mission, the Prime Minister’s Internship Scheme, and collaborative efforts between academia and industry, India is working towards building a skilled workforce, ready to transform Industry 4.0 into a reality. As India’s vision is already shaping up to be the Skill Capital of the world, it should invest in skill development and continuous learning to maintain its manufacturing sector in the era of automation and digital transformation.
Author: Sanjeev Srivastava, Head of Industrial Automation, Delta Electronics India
Disclaimer: The views expressed in this article are solely those of the author and do not necessarily reflect the opinions or policies of ObserveNow Media. The author is solely responsible for ensuring the accuracy, completeness, and validity of the information presented, encouraging readers to independently verify and seek professional advice if needed.